Sanitation scheduling software fills an important role in many different cleaning applications. With food sanitation, effective sanitation software is critically important. Sanitation efforts are essential with poultry, meat, dairy, commercial baking industry, vegetable processing, seafood processing and canning facilities. Scheduling of sanitation activities must be reliable and consistent. Where food safety is concerned, there is no room for error. With this in mind, consider the list below as a means to an effective food sanitation program in a food-processing plant.
- Adequate time to complete equipment cleaning.
- Proper training in sanitation procedures.
- Cross-training sanitation employees for different equipment and work areas.
- Flexible and timely scheduling.
- Integration with maintenance schedules.
- Adequate cleaning supplies.
- Management of unexpected downtime due to improper cleaning procedures.
- Analysis, sanitation reporting and continuous improvement of sanitation efforts.
- Comprehensive documentation and subsequent positive interaction during compliance inspections.
- Ability for non-sanitation employees to formally notify the sanitation department with an electronic sanitation request ticket.
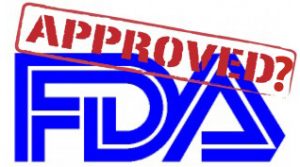
Integrating Sanitation Scheduling with Equipment Maintenance
The first five (5) items listed above are related. Adequate time and proper scheduling means having trained sanitation workers available during planned equipment downtime periods. During vacation and sick leave situations cross-trained sanitation workers cover absent employees. Maintenance and sanitation coordinate their tasks during planned equipment downtime periods. Each of these departments should augment the other if possible. For example, should sanitation clean first making it easier for maintenance to perform their preventive maintenance (PMs)? Alternatively, should maintenance work be performed before sanitation? This type of coordination requires a good relationship between maintenance and sanitation.
Unfortunately, this is not often the case in the real world. In some cases, it makes sense to have one manager over both maintenance and sanitation departments. Indeed, managing maintenance and sanitation scheduling from the same software solution is the best scenario. At the very least, these two scheduling tools should “talk” to each other. Our sanitation scheduling software (CMMS software) has the ability to manage both maintenance and sanitation. Both of these tasks reduce the actual production or manufacturing process but without them, the manufacturing process may stop through breakdown or contaminated product.
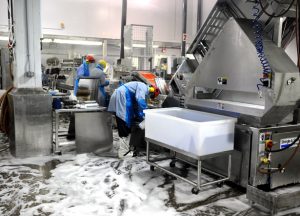
Sanitation Supplies and Spares Management
Having adequate spare parts and cleaning supplies is another facet of the food sanitation. Our sanitation scheduling software system provides a complete inventory and purchasing management system. Sanitation work orders come complete with detailed tasks lists and needed supplies to complete the tasks. Furthermore, the location of each supply or spare part is clearly displayed on the work order. Likewise, the work order flags spares that reach restocking level making restocking simple and intuitive.
Improper sanitation or maintenance efforts occasionally lead to equipment downtime. Water is a common cause of equipment failure following the cleaning of food-processing equipment. Safeties and interlocks left in a defeated state also cause downtime. Improper equipment reassembly may delay the next production run as well. All of these factors can lead to costly downtime. Tracking these downtime causes guides the manager in modifying tasks and schedules with the goal of avoiding future downtime. Reporting and analysis of downtime by either maintenance or sanitation is simplified with a good CMMS software solution.
Audit Food Safety Compliance with Sanitation Software
The food-processing industry is very competitive often operating on a thin profit margin. Major orders are lost or won based upon one AIB or other compliance audit. One of the keys to a good food safety-auditing program is the ability document all sanitation work. Additionally record keeping and reporting are especially important when unexpected audits occur. The ability to immediately produce a record of sanitation maintenance work during a specified date period impresses food safety auditors and protects your company from catastrophic losses. Analysis and reporting guides the sanitation manager to improved scheduling and prioritizing tasks. Our sanitation scheduling software goes a step further by integrating maintenance into this equation.
Get Everyone Involved with Food Safety
Lastly, a good sanitation scheduling software system provides a way for non-sanitation personnel notify sanitation or maintenance of issues they notice in the plant. This formal notification through the maintenance management software displays as a sanitation ticket or repair ticket in on the CMMS screen immediately. The CMMS event handler provides another mechanism for notifying the proper managers by email too. Completed sanitation tickets are later available to the original requester to comment on in the form of a “customer satisfaction survey”. The survey questions and ratings are under the control of the sanitation manager or can be hidden completely. If used this survey closes the loop on sanitation requests.
The importance of food sanitation cannot be overemphasized. MaintSmart integrates sanitation with maintenance, if needed or is used simply for the management of sanitation activities. Simplify and organize your sanitation department with this powerful tool.

MaintSmart Software, Inc.,
66164 Homestead Rd.
North Bend, OR, 97459 U.S.A.
+1-541-404-0616