CMMS software originated in the early to mid 1990’s because of the need for a structured and organized way to maintain equipment assets in the manufacturing environment. Initially, CMMS was simply a work order management system. However, over the past 25 years, CMMS has evolved into a complete maintenance management system that has the ability to manage all facets of the manufacturing maintenance program. So, what are the benefits of manufacturing CMMS software? Below are several specific ways that CMMS software benefits the overall bottom line of any manufacturing company.
Download the full version of the software for a free 30 day trial.
Extend Equipment Life with Proper Preventive Maintenance.
Worn out equipment is costly to repair or replace. Indeed, your goal should be to extend the useful life of equipment to its maximum expected life. Consequently, the best way to accomplish this is with a structured and efficient preventive maintenance program. MaintSmart accomplishes this is several ways as listed below:
- Perform preventive maintenance (PM) with list-based PM module or use the full work order system. Our solution defies the one-size-fits-all CMMS mentality with flexible solutions for simple or comprehensive equipment task assignments.
- Create preventive maintenance task lists manually or automatically by schedule or meter. This frees up the maintenance planner and ensures the correct work issuance to the right person at exactly the right time.
- You only need to create preventive maintenance task lists one time. Best of all, preventive maintenance task lists regenerate themselves automatically every time you close PMs. The end result is, time saved and consistency of work issuance.
- The reliability analysis software module leads to increased efficiencies by determining exactly when to perform PM tasks. This prevents under or over maintaining equipment. In other words, streamlining your maintenance program with the appropriate use of resources when and where needed.
Account for Manufacturing Losses (not just maintenance expenses)
Our system accounts for losses on the manufacturing side caused by equipment failure. It is important to note that an equipment failure does not always mean the equipment has completely stopped functioning. For example, an unexpected decrease in product output is downtime too.
MaintSmart accounts for this where no other CMMS does. To clarify, by tracking three components of downtime, it is possible to captures costs such as product loss, overtime on the manufacturing side to remake lost product and other opportunity costs. So why is this important and how does it help the bottom line for the manufacturing company as a whole? The purpose of tracking this opportunity cost value is to guide the maintenance manager in prioritizing maintenance efforts to obtain the best monetary result for the company (not just the maintenance department).
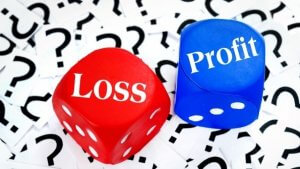
Reduce Equipment Downtime with Manufacturing CMMS Software
Of course, preventive maintenance reduces downtime as noted above. However, it is not always simple to determine the root cause of downtime. Preventive maintenance and repair efforts are wasted or misdirected if the actual source of downtime is not identified. Our Manufacturing CMMS software, unlike other basic CMMS packages, contains a powerful downtime analysis and reporting module to guide the manager in isolating the exact cause of equipment downtime. How specifically, is this accomplished?
- Our flexible equipment failure query analysis tools offer the following: Top Best or Worst Downtime Instances. Here is an example; “what are the top 5% of downtime instances during the past week?” Also included is the Group By analysis component. For example, “what operator shift has the most downtime caused by operator error?” In addition the query tool provides a powerful three-dimensional analysis tool the compared multiple maintenance parameters to one another. For example, “what is the average time down by day of the week compared to maintenance technician?”
- Our CMMS is the only system that uses military standard reliability analysis. Quickly obtain the average failure time for equipment. This referred to as MTBF (mean time between failures). Also, determine the percentage chance of a specific equipment item failing during a specified production run. This KPI is called failure rate. To clarify, failure rate is an objective way to determine how well your PM program is performing and what changes are needed to improve it.
- Use the MTBF (reliability analysis) tool to set preventive maintenance intervals without guesswork.
- Our CMMS base program includes Overall Equipment Effectiveness (OEE). Most software vendors sell an OEE program as a standalone. We offer this power KPI generator with the software at no extra cost. With this powerful KPI suite
Proper Management of Inventory Levels is Crucial
Imagine the frustration when a maintenance technician is performing routine preventive maintenance and parts needed for the job are not available. Similarly, have you ever experienced an equipment breakdown and not had the parts needed for the repair on the shelf? Without doubt, both of these scenarios can lead to expensive and unnecessary lost production time. Making it simple for the maintenance technician to record when parts are used helps maintain spares at the proper levels. Indeed, using a system that simplifies restocking also helps to ensure spares are available when needed. Our CMMS software provides this capability. Additionally many reports are available for tracking spares usage trends, physical audits and even cycle count audits.
Check, Confirm and Modify Maintenance Actions and Policies.
The best manufacturing CMMS software offers the ability to report and analyze all data in the system. Additionally, this analysis must display in a manner that is readable and useful for decision-making. Furthermore, it is essential to review downtime and maintenance policies regularly in a fast moving environment where key processes are dependent upon critical equipment. This often leads to, changes needed to preventive maintenance schedules, maintenance procedures or spares stock levels. The CMMS is the centerpiece of these maintenance functions. Changes to the CMMS data should be simple to implement. Nothing is ever “carved in stone” with our maintenance solution. With proper user permissions these needed adjustments to various maintenance policies and procedures is simple and intuitive.
Downtime analysis and reporting video.
Downtime and reliability analysis.
How else does manufacturing CMMS software solve problems?
As previously stated, CMMS software extends the life and reliability of manufacturing equipment. This in turn leads to improved manufacturing efficiencies with a resulting increase in profit. In other words, much of the increase in profit comes from fewer breakdowns, a smoother process and consistency in product.
A summary and a listing of extended capability included in the software is listed below.
A Complete Maintenance Solution
MaintSmart has four (4) primary components as follows:
- Work order and repair ticket management
- Preventive maintenance
- Inventory and purchasing
- Downtime (equipment failure) reduction
Each of these main components has an analysis and reporting module associated with it.
CMMS Utilities
Other utilities included in the base program at no extra charge are as follows:
- Automatic print/email scheduler sends work orders preventive maintenance and most analysis reports automatically using a floating date trigger.
- Event notification system to alert work requesters, alert on excessive downtime and alert on needed spares.
- Drag and drop any data in the entire program and quickly create a report, complete with statistics and chart.
- Microsoft Project style work scheduler.
- Bar codes are available for employees, spares, equipment and work orders.
- The customized CMMS dashboard uses drag and drop for purchase orders, purchase requisitions, purchase approvals, preventive maintenance, work orders and downtime. (based on user permissions)
- The CMMS program translates into any language.
- All data links back to the equipment asset. There are extensive reports available on cost of equipment.
- Export any data to Excel or web page with two button-clicks.
- Since most manufacturing uses PLCs or man machine interfaces to control and track equipment performance, MaintSmart can connect to this equipment on the plant floor through an OPC interface. Equipment on the plant floor feeds data to the software and the CMMS responds with automatic work orders exactly when needed.
The manufacturing environment is where CMMS began. Today, more than ever, good manufacturing CMMS software is imperative.
Contact us for a free no obligation online demonstration of this powerful CMMS software.
+1-541-404-0616
Skype: "maintsmart"