CMMS software training with videos is a quick way to learn the basics of the subject. Contact our expert trainers for personalized training using your live data or a sample database. Visit our You Tube channel for over 100 FREE CMMS training videos.
New CMMS software training sessions for the new MaintSmart 5.0 for CMMS dashboard, event notification system and more. Learn how to customize the KPI dashboard for each user. Also a new ABC analysis and inventory cycle-count audit training coming soon.
Installation and CMMS Program Set-Up
These topics cover configuration that is common to the entire program. Program configuration includes:
- Naming the equipment hierarchy levels.
- General company or organization information.
- Role-based CMMS program permissions.
- Users and passwords.
Instructions for FULL Licensed Users (trial and DEMO users scroll down to next section)
The videos below numbered 1-4 are generally for production users and describe how to create and set-up a SQL Server database for a new MaintSmart installation. Conversely, for trial and demo users it is best to start with the Demo Access database options first by choosing one of the sample database radio buttons on the initial Tip of the Day screen.
1.) CMMS Software Download and Install
2.) Create a SQL Server Database (advanced)
3.) Set Security SQL Server
4.) Changing the Database (optional)
5.) Populating an Empty Database
Instructions for Trial (DEMO) Users.
It is best to use the Manufacturing DEMO database option offered from the start-up screen (Tip of the Day screen). This contains sample data in 10 languages and requires no set-up of configuration.
CMMS Software Training Introduction
Set-Up Equipment Hierarchy
Equipment Set-Up
Equipment set-up topics cover include adding data equipment grouping (equipment hierarchy), equipment groups (equipment class), equipment descriptors and equipment items. Program configuration includes:
- Equipment hierarchy level data.
- Equipment groups and descriptors.
- Working with equipment items.
Basic Equipment Set-Up
How to Use Equipment Options
How to Set-Up Equipment Details
Preventive Maintenance and Task Configuration
Preventive maintenance software training videos instruct on preventive maintenance task groups, tasks and building preventive maintenance lists:
- Task groups and tasks shared with work orders.
- How to use preventive maintenance software shortcuts.
- Linking spares to PM lists.
Preventive Maintenance Shortcuts
Preventive Maintenance Part Links
Using the Preventative Maintenance Software Module
Preventative maintenance software training videos educate on how to use the PM system once it has been configured. This CMMS program, unlike any other, has a module dedicated to calendar-based preventive maintenance. In addition, we offer a complete work order management system too. As such, create and close PMs in either the work order or the dedicated calendar-based PM screen.
- Learn the basics of using the preventative maintenance screen.
- How to close preventive maintenance tasks.
- Learn to print PM lists and the various formats and options associated with printing PMs.
Preventative Maintenance Basics
How to Close PMs
Learn to Print PMs
How to Use Work Orders
Work orders are the basic unit of work in any CMMS software program. Create any type of work as a full work order, including preventative maintenance type work. Create new work orders from work order templates. To clarify, work order templates are boiler-plate copies of existing work orders used to generate cloned work orders. These new work orders are created based upon a triggering mechanism (either a scheduled event or a metered event). Link these work orders to parts lists, file attachments and have up to 2 GB of text data linked to each work order. Additionally, link work orders to PMs and machine downtime (unexpected equipment breakdown) instances.
- Learn the basics of using the preventative maintenance screen.
- How to close preventive maintenance tasks.
- Learn to print PM lists and the various formats and options associated with printing PMs.
Create a Simple Work Order
Print a Work Order
Create a Work Order Template
Our base CMMS solution contains a complete inventory management software module. Conversely, most of our competitors do not provide an inventory management software module with the basic CMMS. Use the inventory management module for managing all spare parts and other inventory. This is a complete inventory management system. In addition to the basic inventory fields (minimum stock, maximum stock, reorder level, reorder quantity, preferred vendor and more) there are also eight user-defined fields. Furthermore, link spares to work orders, preventive maintenance, downtime or just the equipment. Best of all, all spares linked to equipment are listed as a cost against the equipment for reporting purposes. Moreover, spares lists are stored as history so that the maintenance team or maintenance planner can see what spares were used for any type of work at a later date.
The below CMMS software training videos instruct on:
- Basic inventory management.
- Inventory search capabilities.
- Linking spare parts to work.
Request additional online training for more on this topic. Use your own company maintenance database during your personalized online training. Additionally, we will even guide you in building your own equipment and PM database during training.
Learn Basic Inventory Management
Learn Inventory Search Capabilities
Link Spares to Work Orders
Purchase Order, Purchase Requisition Software Module Training
The CMMS contains a complete purchasing software system rivaling ERP systems costing many times what this system costs. Indeed, the power of this purchase order software rests on it's role-based permission system. For example, assign purchasing roles to users in any combination or based upon one role. Alternatively, assign maintenance technicians to a role where they can only requisition parts and nothing else. Conversely, another maintenance team user may approve the line items on the requisition. Yet another person may be a able to create a purchase order and so on. Similarly, assign all roles to one trusted person if needed too.
The inventory spares database automatically updates as spares are received or used. This ensures accurate counts and consequently timely alerts for below minimum stock levels.
Below are a few CMMS training videos that instruct on:
- Purchase requisition taring and RFQ instruction.
- How to approve line items on a requisition for purchase.
- How to create and manage purchase orders.
Request additional online training for more on this topic. Personalized your CMMS training to fit to your company's requirements with your data.
Learn Purchase Requisitions | RFQ
Learn to Approve Requisitions
Instruction on Purchase Orders
Equipment Failure Tracking (Downtime Software Module) Training
Equipment failure tracking is a module unique to MaintSmart. No other CMMS software offers a dedicated equipment failure tracking capability. Best of all, this module guides the maintenance manager not only to the trouble equipment or issues with personnel but also identifies which problems are costing the organization as a whole the most money. Additionally, simple but extensive reporting and charting for machine downtime guides the maintenance planner in prioritizing task assignments. Lastly, reliability analysis and OEE (overall equipment effectiveness) are possible because of this down time collecting capability. This is another powerful feature found only in our CMMS system.
The below videos instruct on:
- Equipment failure tracking (down time) analysis.
- How to use down time reporting functions.
- Instruction on OEE (overall equipment effectiveness).
Request additional online training for more on this topic. Best of all, hit the ground running by using your maintenance team's database during the training sessions. We assist in proper configuration of the maintenance program during training at no cost.
Downtime Analysis Instruction
Downtime Software Reporting
How to Use OEE
Print/Email Scheduler and Other CMMS Software Training Topics
The print/email scheduler automatically issues most reports, including current preventive maintenance tasks, new work orders, directly to email or one or more printers. These schedules are based upon a floating data range defined by the user.
Examples could be:
- Every 7 days print out weekly PMs.
- On the second Tuesday of every month send a down time report with chart to the plan manager but only include down time for past 14 days.
- Create a new work order on the 10th of every month to replace filters in HVAC unit. Include a parts list and SOPs.
The query-builder is available for all data in the entire CMMS. This query-builder is drag and drop and very simple to use and benefit from. A corresponding chart is created automatically with queried data.
Additional CMMS training videos include:
- Learn to create automatic work orders from the scheduler.
- How to create automatic work orders from meters.
- Configure the meter and equipment maintenance scheduler scanner.
- Email sender configuration, default email sender and CMMS automatic emailing job.
Request additional online training for more on this these special topics. Online training may be personalized to your company's requirements and can be presented with your data.
How To Use the Automatic Print and Email Scheduler
How To Use the Report-Builder (CMMS OLAP Tool)
Automatic Email Notifications on Work Order Status Change and More
Automatic Work Orders
Meter and Schedule Scanner Set Up
How To Set Up the CMMS Dashboard
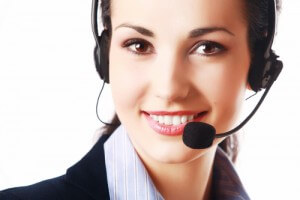
Contact us for personalized CMMS software training. Our online trainer can set-up your company then create equipment, tasks and personnel. We can have work orders and PMs for at some equipment producing real results within the two hour training period. We'll even send the training database to the trainee to use in your maintenance operation. This is the best way to immediately prove that our maintenance management software solution works.
MaintSmart Software, Inc., 66164 Homestead Rd., North Bend, OR, 97459 U.S.A.
+1-541-404-0616 ~ [email protected]